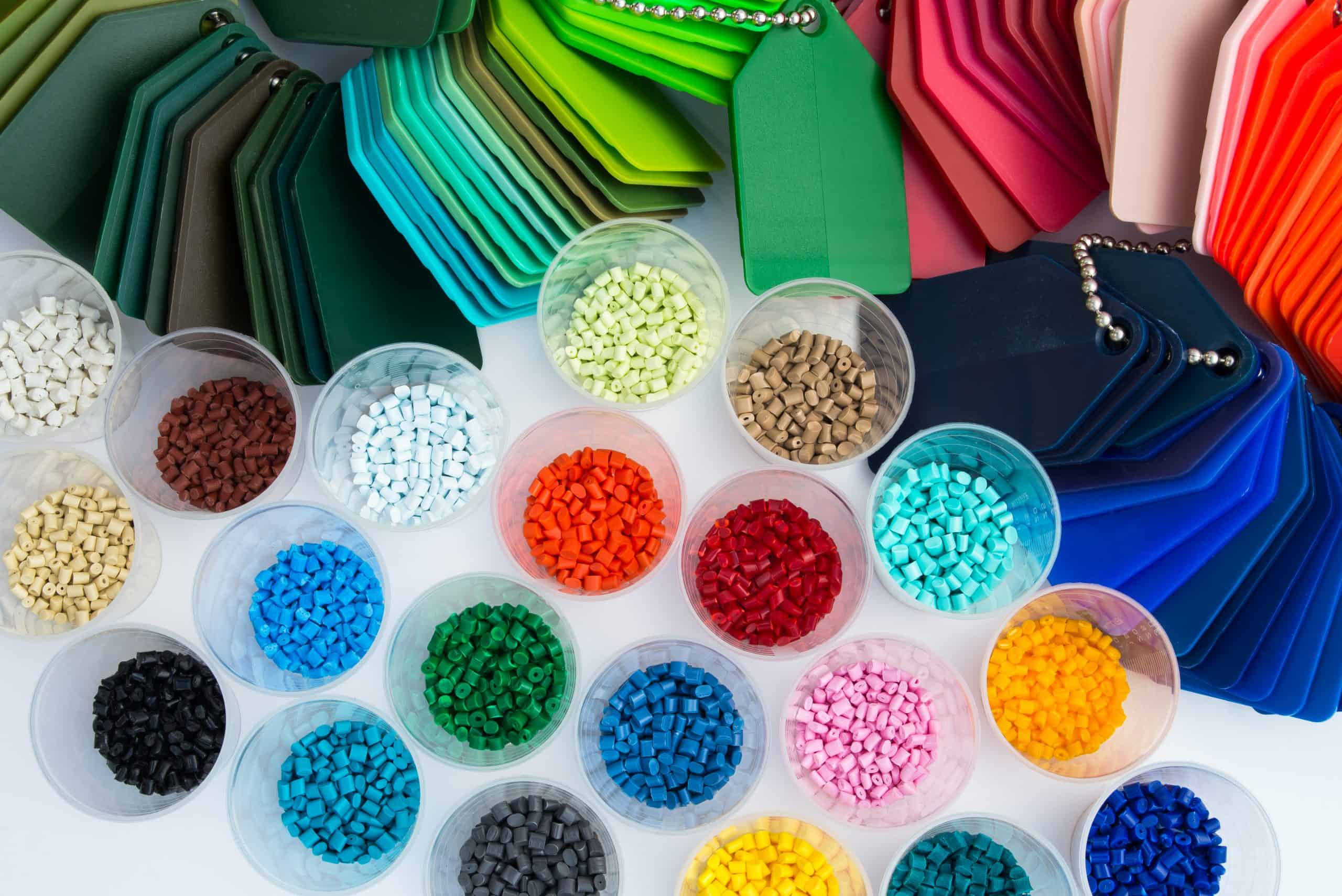
A large family
Plastics comprise a large family of materials which can be classified into various types. Learn more about the different kinds of plastics and their particular applications and benefits.
Circular plastics
These are a group of plastics fully or partially produced from circular feedstocks. Circular feedstocks describe feedstocks linked to system circularity, where a connection from end-of-life (e.g. waste) to start-of-life (new product) can be created. That can be achieved via different loops (biological and technical) of a circular economy. Circular feedstocks include bio-based, recycled and carbon-captured-based feedstocks.
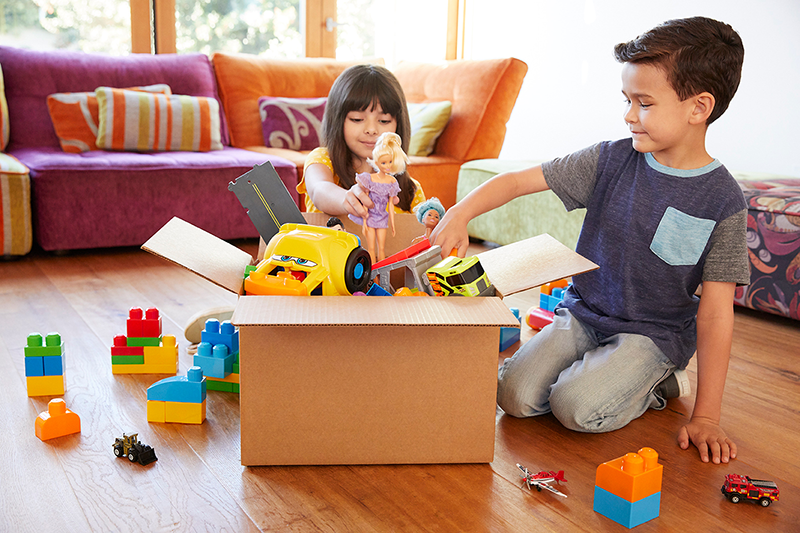
Recycled plastics and carbon captured
Although the term ‘bioplastics’ is widely used, it can often refer to two entirely different properties of plastic materials, namely plastics using a bio-based feedstock (origin of carbon) and plastics that are intrinsically biodegradable under one or more environmental conditions (end-of-life).

Bio-based plastics
Bio-based plastics are plastics fully or partially produced from bio-based feedstock. Bio-based feedstocks are raw materials of biological origin grown and naturally replenished at a human time scale, excluding materials embedded in geological formations and/or fossilised. It can be produced from grown crops (so-called ‘first-generation’ such as maize, rapeseed, etc.) or organic residuals and waste (‘second-generation’ such as agricultural waste, frying oils, and manure).
Plastics with attributed bio-based content are called bio-attributed plastics. The determination of the bio-based content can be done via feedstock attribution.
Compostable and environmentally biodegradable plastics
Biodegradable polymers can be used to create plastic materials and applications accessible for microbial consumption, meaning decomposition by naturally occurring (micro)organisms. Therefore, the common characteristic of all biodegradable plastic applications is to achieve “microbial conversion of all its organic constituents to carbon dioxide, new microbial biomass and mineral salts under oxic conditions, or to carbon dioxide, methane, new microbial biomass and mineral salts under anoxic conditions.
There is a difference between certified compostable and environmentally biodegradable plastic applications. These two plastic application types have different biodegradation needs, end-of-life receiving environments and sustainability value propositions.
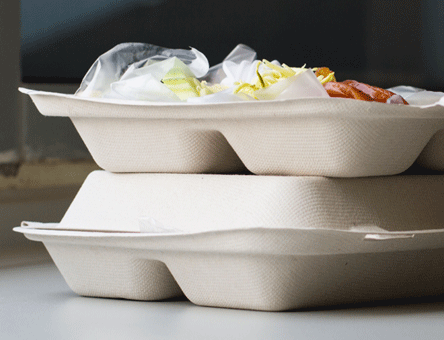
Compostable plastics
The recycling of bio-waste as a disposal method significantly lowers European GHG emissions compared to incineration or landfill, and the application of mature composts plays a significant role in restoring the biodiversity and fertility of agricultural soils.
Certified compostable plastics in specific applications have been demonstrated to support the quality of the collected household bio-waste. Compostable products benefit bio-waste collection by limiting conventional plastic contamination; e.g., compostable materials can replace applications often accidentally sorted in bio-waste.
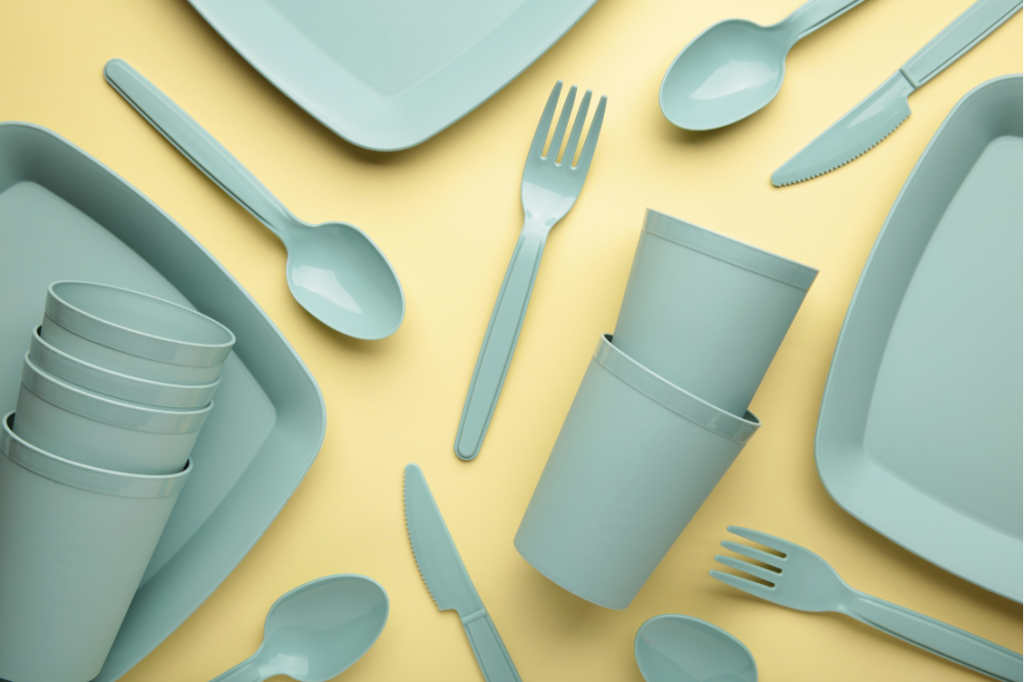
Environmentally biodegradable plastics
Environmentally biodegradable plastics are fully biodegraded by the microbiota present in specific matrices, such as agricultural soil or freshwater. These types of biodegradable plastics are tested and certified for biodegradation only in these particular matrices – which means a soil-biodegradable item may not achieve the same level of degradation in a different environment, such as seawater. Considering this, environmental biodegradation should never increase litter volume or be an excuse for improper disposal.
Engineering Plastics
Engineering plastics exhibit higher performance than standard materials, making them ideal for demanding engineering applications. In many applications, they have gradually replaced traditional engineering materials such as wood or metal. This is because they equal or surpass them in their weight/strength ratio and are much easier to manufacture, especially in complicated shapes.
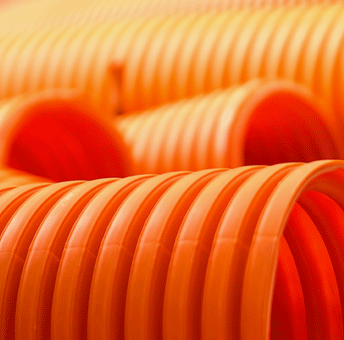
Expanded polystyrene
Expanded polystyrene, or EPS, is a widely used commodity polymer. It has been a material of choice for over 50 years because of its versatility, performance and cost-effectiveness. It is commonly used in everyday applications, such as chilled produce boxes, bicycle helmets and insulation material.
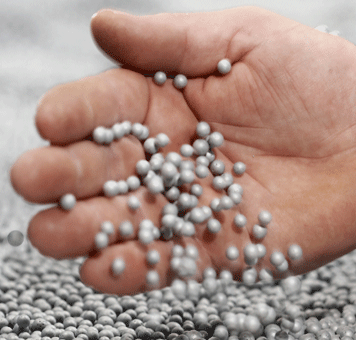
Thermosets
Thermosetting polymers, often called thermosets, have been around for more than 50 years and are one of the most successful plastics families. Thermosets are a type of plastic formed by permanently hardening a soft solid or liquid prepolymer (resin) through a process called curing. Curing is initiated by heat, radiation, high pressure, or the addition of a catalyst.
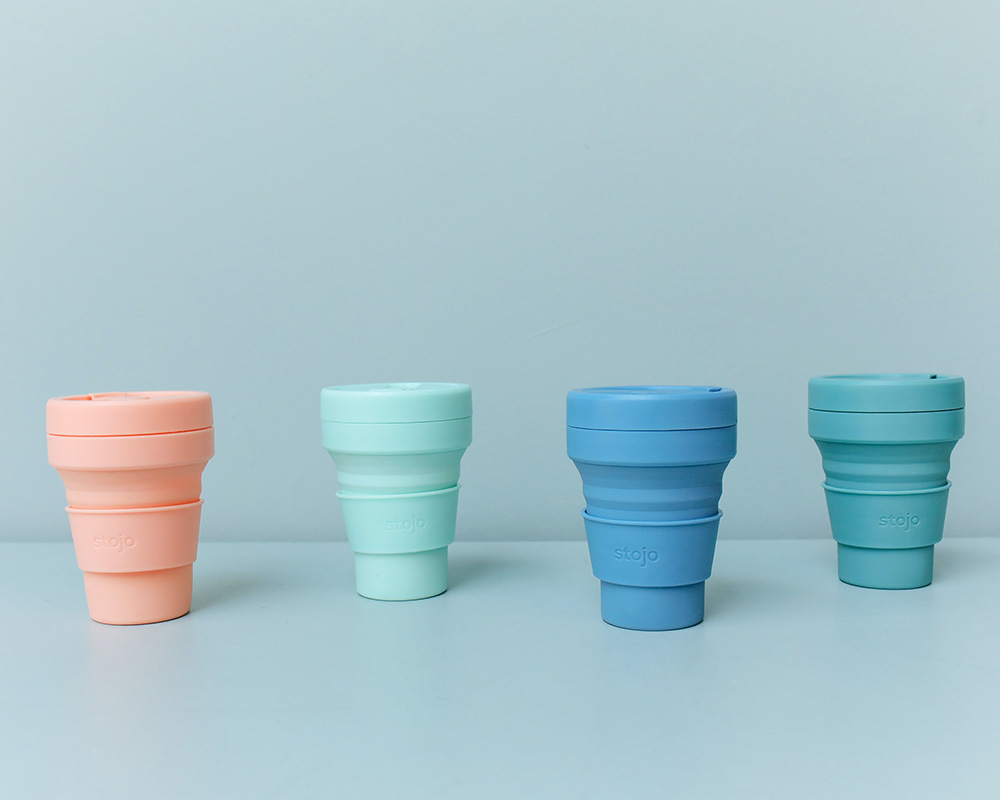
Fluoropolymers
Fluoropolymers are renowned for their superior non-stick properties, associated with their use as a coating on cookware and as a soil and stain repellent for fabrics and textile products. They also contribute to significant advancement in areas such as aerospace, electronics, automotive, industrial processes (chemical and power sectors, including renewable energy), architecture, food and pharma and medical applications. The most well-known member of the fluoropolymers family is PTFE (polytetrafluoroethylene).
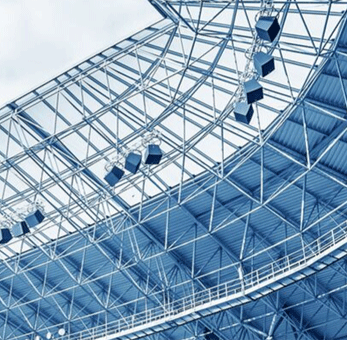
Polyolefins
Polyolefins are a family of polyethylene and polypropylene thermoplastics. They are produced mainly from oil and natural gas by polymerising ethylene and propylene. Their versatility has made them one of the most popular plastics in use today.
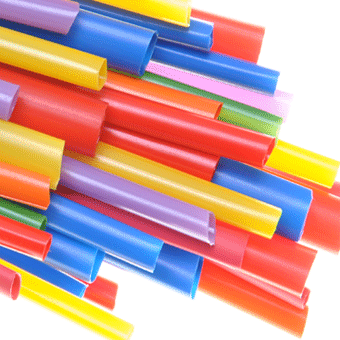
Polystyrene
Polystyrene is a synthetic polymer made from styrene monomer – a liquid petrochemical. It is a thermoplastic polymer which softens when heated and can be converted via semi-finished products, such as films and sheets, into a wide range of final items.
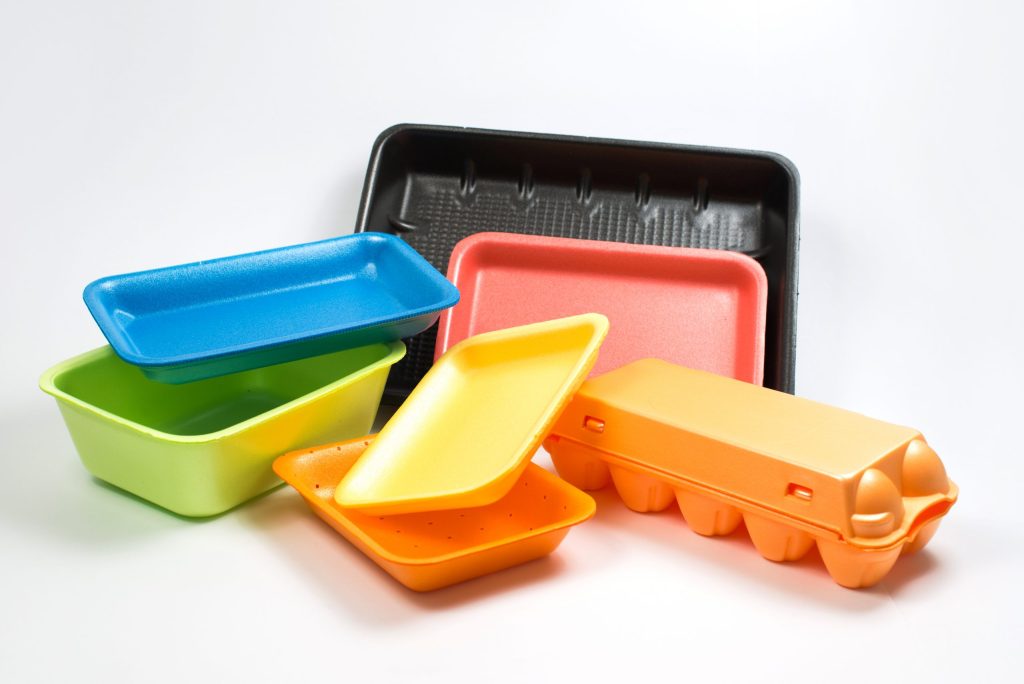
Polyurethanes
Polyurethane (PUR) is a resilient, flexible and durable manufactured material. There are various types of polyurethanes, which each look and feel very different. They are used in an extensive range of products. Polyurethane-containing products surround us in every aspect of our everyday lives. While most people are not overly familiar with polyurethanes because they are generally hidden behind covers or surfaces made of other materials, it would be hard to imagine life without them.
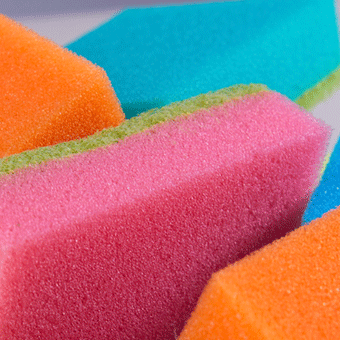
Polyvinyl chloride
Polyvinyl chloride (PVC) was one of the first plastics discovered and is also one of the most extensively used. It is derived from salt (57%) and oil or gas (43%). It is the world’s third-most widely produced synthetic plastic polymer after polyethylene and polypropylene. PVC comes in two basic forms: rigid (sometimes abbreviated as RPVC) and flexible.
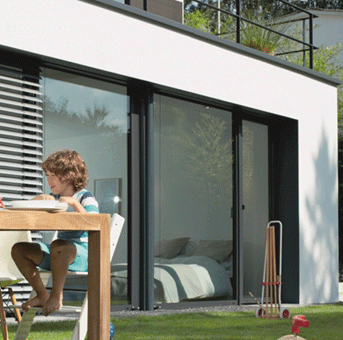
Thermoplastics
Thermoplastics are defined as polymers that can be melted and recast almost indefinitely. They are molten when heated and harden upon cooling. When frozen, however, a thermoplastic becomes glass-like and subject to fracture. These characteristics lend the material its name and are reversible so that it can be repeatedly reheated, reshaped. As a result, thermoplastics are mechanically recyclable. Some of the most common types of thermoplastic are polypropylene, polyethylene, polyvinyl chloride, polystyrene, polyethylene terephthalate and polycarbonate.
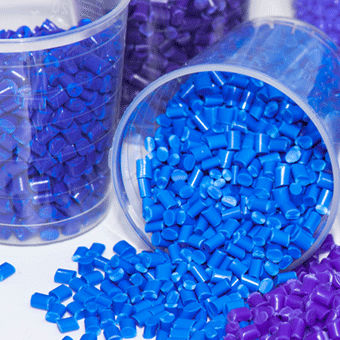